Get caught up with the step-by-step series
Part 1: Build an AR-15: The Series IntroductionPart 2: Build an AR-15: AR Calibers
Part 3: Build an AR-15: Direct Impingement or Piston Operation
Part 4: Build an AR-15: Tools and Materials
Buy an AR-15 Lower Receiver on GunsAmerica: http://www.gunsamerica.com/Search.aspx?T=ar-15%20lower
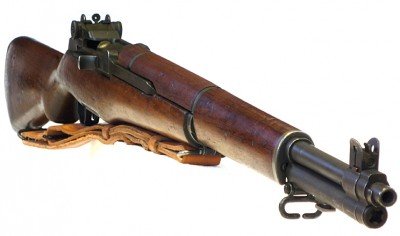
The Garand continues to be popular thanks to groups like the CMP and Call of Duty games. But it wasn’t the logical choice for the wars of the late 20th century.
A brief and reductive history
As the dust settled from WW2, the powers-that-be accepted that our standard service rifle wasn’t the answer for unconventional warfare. The M1 Garand was simply too big, too slow, too limited. Battle rifles were a product of late 19th and early 20th century fighting styles. While there are a lot of die-hard fans of the Garand, most of them would hesitate to carry the weapon into war.We had fielded the M1 Carbine, which was easier to carry, but the .30 Carbine round had limited range and mediocre ballistic performance. There was a need for a rifle that took the best features of all of America’s sweet hearts and embodied them into one space age blaster.
But tradition dies hard. We had a brief detour with the M14, essentially a Garand-like rifle that used a box magazine and fired a slightly smaller round (.30-06 and 7.62×51). The prevailing belief suggested that we needed a rifle that fired a heavy projectile.
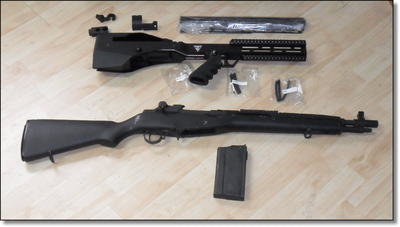
Even with significant upgrades (like the Juggernaut Rogue Bullpup Chassis), the M1A (Springfield Armory’s version of the M14) is a beast. Capable, yes, but in a different class than the slimmed down AR-15.
The rifle was sold to civilians as the AR-15 and was heavily marketed to the US military (and eventually adopted as the M16). In 1967, the M16 was officially adopted as the US Military’s service rifle. And it wasn’t a smooth adoption. For more on the controversy surrounding how the M16 launch catastrophically failed, I’d suggest reading C.J. Chivers’ book The Gun.
Rails, shorter barrels, flat top receivers, collapsible stocks, pistons… the weapon system changed as time progressed. One part, though, has remained fundamentally the same (at least until recently). The lower receiver is the heart of this gun and it is the reason why this rifle is still America’s weapon of choice.
So what is a lower Receiver?
This is for all the CNN reporters who butcher these simple definitions. The lower receiver of an AR-15 is a more than a part; it is the single piece that every other part revolves around. Modular rifle design developed to adapt to the changing needs of individual soldiers. Lowers are (supposed to be) universal and the parts that go in and on them are interchangeable. Triggers are held in place by cross pins. Parts like stocks, buffer tubes, pistol grips, and selectors all come together to form the fully functional lower.Why buy just a lower?
In today’s market, most people buy lowers with uppers as complete rifles. But we’re looking at a different route and building the guns to our exact wants and needs. As everything revolves around this one piece, we thought we’d show it some love. There are four main ways lowers are sold:- Complete rifles (I know of very few people who make their rifling buying choices based on the design of the lower, but it can happen. LWRC, for example, has a stylized lower that has drawn fans)
- Complete lowers (these have all of the guts intact–trigger, controls, etc. Minimal DIY)
- Stripped lowers (while these are ready to be built, they allow for more customization)
- 80% lowers (for advanced DIY enthusiasts–more on these below)
Buying a complete lower
Buying a complete lower is a great way to go if you don’t have the tools or know-how to assemble your own gun. You can get them from your favorite manufactures. Palmetto State Armory is popular with those looking for reliability at a low price. With endless options and the Internet at your disposal, you can find a lower that is built exactly the way you want it. These lowers can be purchased online and then shipped to your local FFL for transfer on the old 4473 form you would use to buy any gun. If you are looking for some semi-custom choices, but are not ready to dive into amateur gunsmithing, then this path is for you.Buying a stripped lower
What if you want more options? Say you like the looks or feel of one lower, but want a specific design to the trigger shoe on your two-stage trigger, and no one is selling that as part of a package deal? Buy a stripped lower and build it yourself. This is the best way to go if you want to build a rifle with only the best components.It’s also a great way to go if you want to build a rifle on a budget. Stripped lowers can be had for a song–sometimes below $50. As the lower isn’t immune to the whims of firearms fashonistas, they can range into the hundreds of dollars. For your first build, keep it simple. As you learn the ins-and-outs of controls, mag-well shapes, the relative weights of component parts, then you can swap out the simple lower receiver for one that does exactly what you want.
Head my warning though–if you are looking to build a budget gun and don’t have much experience, assembling a lower can be a daunting task. Know your skill level. Remember that these are modular in design, and that parts are supposed to fit. Don’t remove material. Don’t force anything. Gunsmiths aren’t cheap. Check out the options like the DSA pictured above–clean, simple, priced right, and completely customizable.
A quick detour into material construction
While we’ve been looking at the basics of how these are sold, we’ve skipped over an important aspect of design. Most are built from varying grades of aluminum. The material is strong enough, easy to work, doesn’t rust, and light. And if it does break, the part is easy to replace. Yet there’s more to consider.Cast lowers: some lowers are milled out of aluminum that has been melted and poured into a basic mold. While expedient, this method produces a loose crystalline structure within the aluminum. Is it strong enough? Yes. Is is the strongest method? No.
Milled lowers: while most lowers are milled at some point in their construction, some are milled from billets of aluminum. A billet is just bar stock. The strength of the bar itself (which is determine by how it is made) determines the strength of the final product. This method often produces a stronger lower than simple casting.
Forged lowers: if you want something more, look to forged lowers. These are made from billets that are hammered into molds, or compressed under pressure. This forging is then milled. The compression of the crystalline structure makes this one of the strongest methods of construction.
If you are looking at aluminum, consider the end cost. More strength equals more production time. Is it worth it? Maybe. It depends on the intended purpose of the gun. If you want even more strength (or even less) there are other options. What other materials are common? Just about everything.
For those who want an AR to look at, I’d suggest Turnbull’s TAR-15. It is made of steel. That’s kind of like saying the Hope Diamond is made from coal. Turnbull makes some pretty guns. If you’d rather not lug around ferrous metals, you can try carbon fiber. Tegra Arms makes light-weight lowers out of our generation’s space age materials. The one above is a carbon fiber composite, which means the polymer is reinforced with an incredibly light and durable material.
Or maybe you want titanium? You know–why not have a rifle that will outlive you, and your kids, and your kids’ kids…. These will likely have the same service life as a 1950’s Russian AK. Nemo Arms, a company that pushes the limits on the AR pattern rifles, has an AR-10 made from titanium. Why not an AR-15?
Maybe because it is overkill. Plastics work fine. Polymer lowers have been a thing of novelty in the past, but in recent years polymer technology has advanced to a point that the polymer lower is a viable option. These lowers can handle serious use and cost even less than a stripped aluminum lower. Tennessee Arms Company is a leader in this field as they have developed an entire line of polymer lower receivers reinforced with marine grade brass where strength is necessary. These lowers are inexpensive, hold a lifetime warranty, and are about as cool as they get. And some hold the opinion that the plastic lowers flex where aluminum lowers crack.
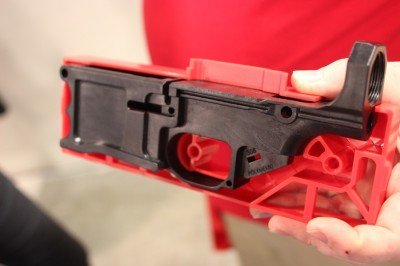
The
polymer reacts better, we’re told, than some metals. It has more
elasticity, and handles recoil energy without cracking. And the jig
shows what needs to be removed to make it work.
Buying a 80% lower
http://www.80percentarms.com/collections/lower-receiversLowers that are serialized and considered by the ATF to be firearms must be transferred through an FFL, at least originally. What if you want to skip that step? 80% lowers may be the best option. If a lower is only 80% complete, it is not yet a firearm. Therefore, it requires no special paperwork. It can be bought from a manufacturer and sent directly to you.
You finish the last 20%, and make it into a functional lower receiver. How hard is that to do? It takes a bit of skill, but it is hardly an advanced project. If you can operate a drill press and are confident in your ability to measure things correctly, the job is easily accomplished.
They come in polymer, from folks like Polymer80 and in Aluminum from 80percent arms.
Read our reviews of the 80% build processes here:
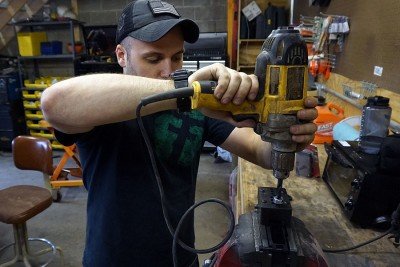
Once you get a handle on the basics, you may want to mill your own lower. Aluminum is harder to cut than plastic.
The flip side to this coin is that the lower you manufacture is truly your gun. You are the manufacturer. It is un-serialized, and something you can show off to your friends for years to come. Building out a 80% lower does require time and a bit of skill, but if you are reasonably good with power-tools, there is no greater reward than building a gun around a lower receiver you milled yourself.
In the end
Once you’ve decided on how much time and work you want to put into a lower, and what materials you are looking for, you can fine-tune the process. While most lowers are the same basic shape, there are nuances that can be important. Do you want or need a left-handed design? A right hand orientation with ambidextrous controls? Are you looking for a wider mag well to make loading easier? Would you prefer grooves on the front of the mag well for support hand grip? How much decoration do you want on the lower itself? Do you risk sacrificing durability for weight reduction and go with a skeletonized lower that is feather light?The AR-15 is everything it can be because of the lower. There have never been more options than there are today. Find what appeals to you and be honest with yourself on what you are comfortable and capable of taking on.
No comments:
Post a Comment